Case Study – University Test Tank
Problem: A technical university had a marine engine testing facility with multiple test tanks in interior and exterior rooms. The discharge from the engines was causing the water to get dirty so that the university was spending between $15-20,000 per quarter hauling water!
The interior rooms had sets of test tanks that could be manifolded together to be treated as one. The outside rooms did not lend themselves easily to manifolding the tanks together. They called us to develop a solution that would allow them to either treat and discharge the water to the sewer or recycle the water with no discharge.
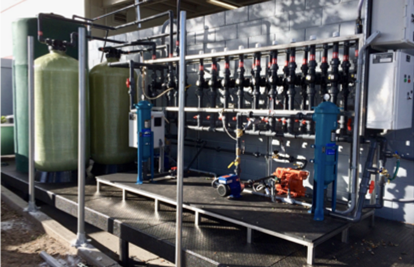
Solution: After analyzing available options, we engineered and installed a single water recycling system adjacent to the building that was capable of receiving the water from all of the tanks at different times, removing the oils from the water, disinfecting the water, and returning the water to the respective tank system.
The tank manifold systems in the interior rooms are individually piped to the recycling system with a supply and return line. These attach to a dedicated automated valve system that is programmed to periodically select a specific tank system, draw out the water through the system and return it after treatment to that tank system. The PLC insures this sequence occur on a pre-determined schedule.
Piping drops were installed in the outside rooms so that a technician can manually place an oil skimmer assembly with an integrated suction/discharge hose assembly into any tank and send that water through the recycling system. A remote control panel allows the technician to start/stop the recycling system and to select a time period for the recycling to occur. Processed water passing through the recycle system is free of particles greater than 10 microns in size, substantially all emulsified oils, waxes and other volatile organic compounds.
The engineers at the university tell us that they are saving money and the system constantly “exceeds expectations”!