
Oil Water Separator Media
In many washing applications, solids are a main component of the washing process. Heavy solids such as rocks and muck are often washed off and fall onto the wash pad where they can be easily removed. Other, finer settleable and suspended solids, however, often become entrained in the oily wash wastewater. Separating these settleable or suspended solids from the oily wash water is critical so that they do not clog the separator media and interfere with the oil water separation process.
To insure our oil water separators work well in a high solids environment without clogging, we have introduced a new coalescing media with a corrugated, cross-flow design.
This new media design is both unique and simple. As the water enters the separator, the flow is directed evenly across the surface of the media plates. The solids are captured and fall to the trough area of the corrugated plates below and the oils rise and stick to the trough area of the plates above. This design maintains laminar flow throughout the media so the oil and solids do not remix. Since the plates are smooth, the solids slide down the corrugated plates to the hopper area where they can be easily removed. Separated oil flows upwards along the plates to the top of the separator where it can be removed.
- Available in stainless steel, PVC, HPVC and polypropylene
- Plate spacing of ½”, ¾” or 1 ¼” depending on application
- Supplied in blocks for easy installation and removal
By coupling high efficiency separation with easy maintenance, this new media will ensure your oil water separator
operates at peak performance for years to come.
Give us a call at 800-453- 8639 for more information!
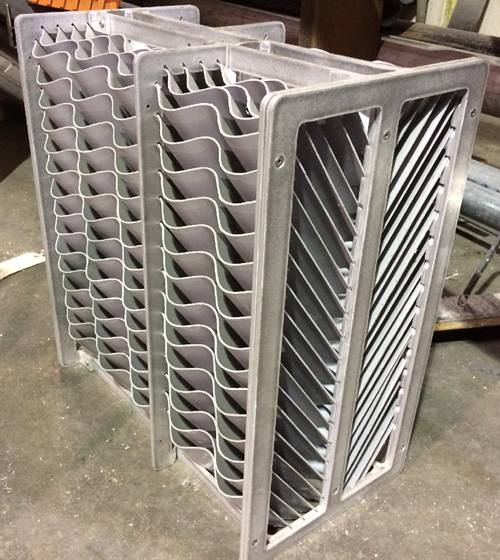
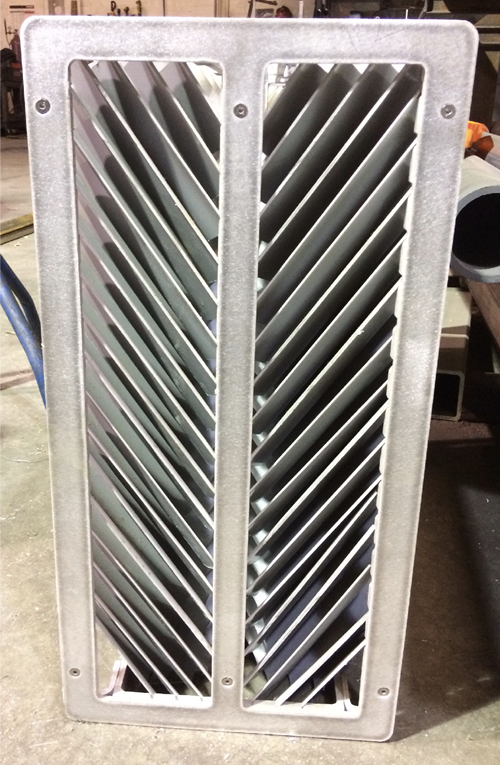