In some applications with extensive contamination, a simple oil water separator is simply not enough to treat the water prior to sewer discharge. Our heavy-duty MM-Series treatment systems treat wash water in multiple stages so it can be safely discharged to the sewer or, in many cases, the surroundings.
Stage 1 – Solids Settling
Almost all commercial washing operations produce some solids so the first stage of our filtration process is the solids handling system. We help you develop site-specific solutions to eliminate as many solids as possible before running the water through to the next stage of filtration. Solutions include custom-designed sumps, basins, trenches or screening systems.
Stage 2 – Oils & Solids Separation
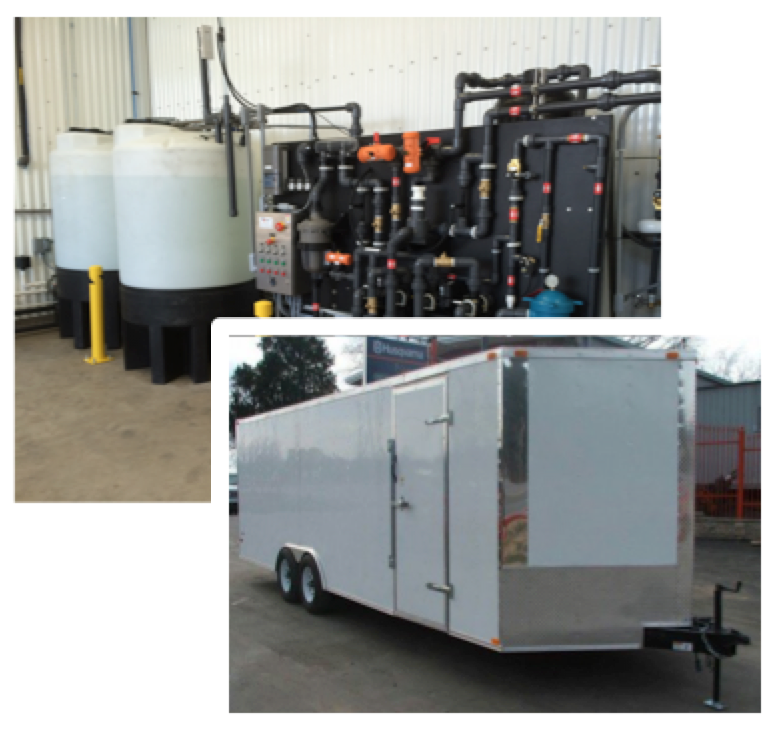
After the coarse solids settling, the water is processed through either a multi-compartment stainless steel oil water separator or a stainless steel clarifier oil-water separator, which separates out smaller suspended solids, oil and water. In the first compartment of the clarifier oil water separator, free oils float to the surface. In the second section, the stainless steel clarifying plates remove coarse amounts of oil from the waste stream and remove as much Total Suspended Solids (TSS) as possible. The angles of the non-clogging plates are 55° which will allow any solids to slide down the plates into the solids hopper, where they can easily be pumped out. Finally, the coalescing media removes essentially 100% of all free and dispersed non-emulsified oils so the FOG effluent concentration can be as low as 5 ppm.
Stage 3 – Water Filtration & Polishing
After the clarifier oil-water separator, the water is pumped though a multi-media (sand, gravel, anthracite) filter and then safely discharged to the sewer or surroundings. Processed water passing through the system will be free of substantially all emulsified oils, waxes and other volatile organic compounds with only limited soaps and detergents remaining in the treated water. If needed, a blended activated carbon or a carbon/clay mixture tailored to a particular waste stream can be added as an optional polishing filter.
System Features
- Non-Ferrous Construction – Stainless Steel, PVC
- Fully-Automatic, pre-wired
- Clarifier Separator System
- Stainless Steel Clarifier Oil/Water Separator with 55° Hopper
- Advanced European coalescing media designed to remove oil droplets greater than 20 microns
- Electric or Air Diaphragm pump with controller
- Discharge Filtration System
- Automated Self-Cleaning Multi-Media and/or Clay/Carbon Fiberglass Filter Tank
- Heavy-duty, high efficiency Pump
- Sensors and interconnecting Schedule 80 plumbing
- NEMA-4X control panel
- PLC controller for automatic back wash operations
- All components mounted on heavy-duty stainless steel skid
Depending on the location, many options are available to maximize the efficiency of the wastewater treatment system including:
Optional Features
- Can be configured with existing equipment
- SCADA and remote monitoring UL/CSA Listing
- Transportable equipment rooms
- Rain Diverter Systems
- Chemical/Acid/Salinity Resistant Pumps & Components
- pH control system
TYPICAL MM-SERIES SYSTEM SPECIFICATIONS
MODEL |
MM-10/10 |
MM-35/20 |
MM-65/50 |
MM-100* |
DESIGN FLOW RATE, GPM |
1-10 |
1-25 |
10-55 |
30-100 |
COALESCING PLATE AREA, SF |
41 |
124 |
211 |
400 |
COALESCING MEDIA, CF |
4 |
8 |
24 |
48 |
CLARIFIER SEPARATOR SIZE, FT (WxLxH) |
3 x 7 x 5 |
3.5 x 8 x 6 |
4 x 10 x 6 |
5 x 11 x 7 |
NON-EMUSIFYING INFLUENT PUMP, GPM MAX |
20 |
50 |
75 |
125 |
MULTI-MEDIA, LBS |
300-500 |
500-1000 |
2500-2600 |
3700-4200 |
OPTIONAL POLISHING CLAY/CARBON, CF |
4-15 |
10-40 |
20-40 |
40 |
FILTER PUMP, HP |
1.5 |
2 |
3 |
5 |
DIRTY WATER STORAGE VOLUME, GAL |
500-750 |
500-1000 |
750-1000 |
1000-1500 |
CONTROL SYSTEM |
PLC, Automatic, Manual or Off |
|||
PUMP FRAME SIZE, FT (WxLxH) |
3 x 6 x 6.5 |
3 x 8 x 8 |
||
POWER REQUIREMENTS |
208 / 240 V 1 ph or 208 / 240 / 480 V 3 ph |
* LARGER CAPACITY SYSTEMS (200-1500 GPM) ARE AVAILABLE
APPLICATIONS:
- Commercial Trucking
- Locomotive
- Mining
- Marine
- Forklift
- Oil and Gas Drilling