Sanitizing Foggers
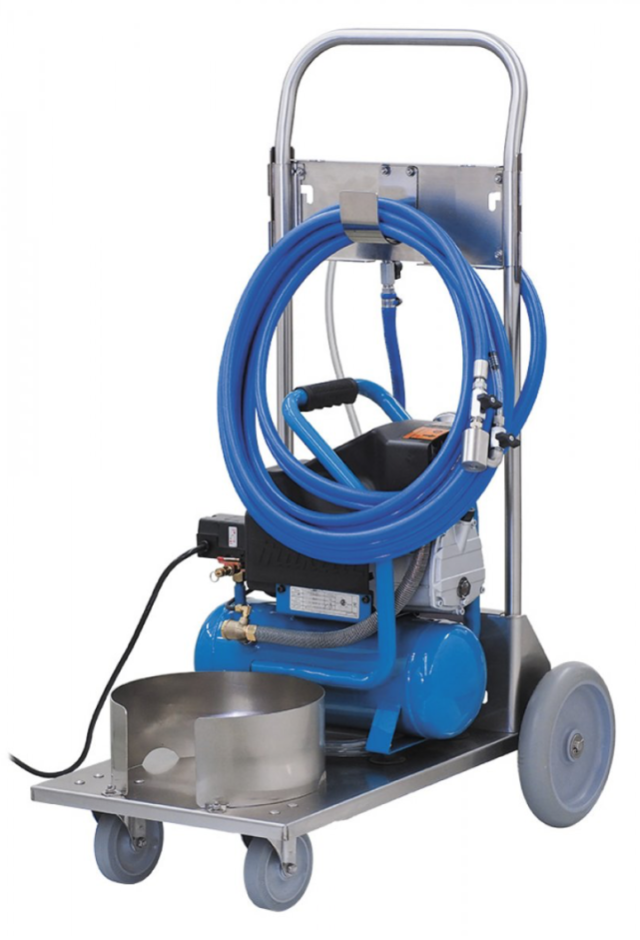
Foggers were typically used for sanitation in food and beverage facilities. Today, however, foggers and atomizers are now being used to easily apply disinfectants and sanitizers to hospitals, schools, hotels, airplanes, cruise ships, warehouses and public transit facilities.
Using compressed air, foggers atomize ready-to-use chemical disinfecting solutions and project the fog/mist particles into the air or onto exposed surfaces.
Foggers produce dry to wet fog, and come in range of models and sizes from small hand-held models to portable systems to permanent-mount, inline systems that can project particles up to 25 feet in 8 directions! Let our engineers help you design the optimal fogging system for your facility.
Self-Contained Portable Fogger Cart
Our Portable Fogger Cart is one of our most versatile models – perfect for schools, hospitals, doctor’s offices and hotels. Powered only by a standard 120V electrical connection, this portable, self-contained system comes complete with a quiet on-board compressor, fogger body, hose and thumb-gun on a stainless steel cart. With the thumb-gun, it allows you to deliver chemical fog precisely where you need it.
The system uses compressed air to draw pre-diluted chemical solution from a pail on the cart to the fogger body which atomizes the chemical and projects it as small to medium size “damp” particles at distances up to 15 feet. Fog (mist) fills the air and saturates exposed surfaces, including hard-to-reach areas. Just plug it in and go!
Features
- Stainless steel fogger body
- 120V air compressor
- 25′ twin-line air/chemical hose with activation ball valves
- 10 color-coded precision metering tips can refine the particle size by reducing chemical usage
- Stainless steel, 4 wheel cart assembly with hose rack
- Non-marking tires with stainless steel swivel casters
- Stainless steel metering tip holder
- Stainless steel construction ensures durability and years of outstanding performance
Portable 2-4 Way Fogger
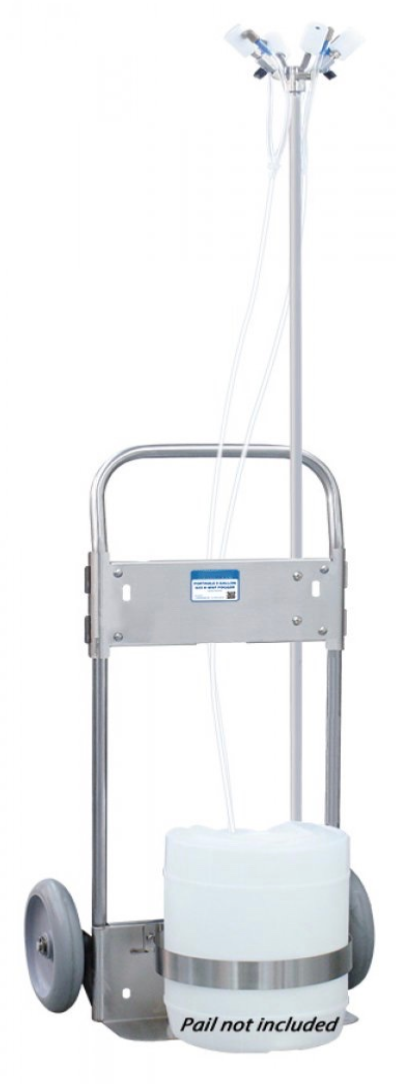
The Portable 5 Gallon 2-4 Way Fogger is a chemical atomizer that uses compressed air and
venturi action to draw ready-to-use chemical solution from a 5 gallon pail on the cart through a
telescoping mast to the fogger body which atomizes the chemical and projects it as small to
medium size “damp” particles at distances up to 15 feet. Fog (mist) fills the air and saturates
exposed surfaces, including hard-to-reach areas.
Ball valves on two fogger bodies allow for conversion to 2-Way
fogging for narrow areas and the telescoping mast allows for
variable height adjustment up to 80 inches.
You can refine the particle size for your particular application
and manage chemical use by choosing different optional precise
metering tips.
Features
- (4) Four polypropylene fogger bodies mounted on adjustable mast
- (2) Two air ball valves to control air flow
- (2) Two 10′ chemical suction tubes and strainers
- (4) Four metering tip holders
- Stainless steel 2-wheel cart with non-marking tires
- Round stainless steel 5 gallon pail rack (square rack optional)
- Stainless steel, adjustable height fogger mast
Compact Hand-Held Fogger
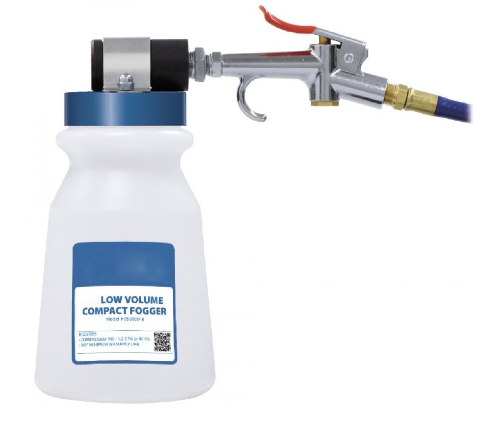
The Compact Hand-Held Fogger is a chemical atomizer that uses compressed air and venturi
action to draw pre-diluted chemical solution from the attached bottle, atomize the chemical, and
project it as small to medium size “damp” particles at distances up to 15 feet.
It is easy to use! Just fill the bottle with your pre-mixed chemical/disinfectant, connect compressed
air, and press the thumb gun activator. Fog/mist will fill the air and saturate any exposed surfaces,
including hard-to-reach areas. You can refine the particle size and manage chemical use by
choosing the correct precise metering tip for your particular application.
Features
- Polypropylene fogger body attached to bottle top
- Lightweight wide-mouth, polyethylene quart bottle
- Thumb trigger gun with easy air hose connection
- 10 color-coded precision metering tips
- Metering tip holder
Pump Fed Foggers
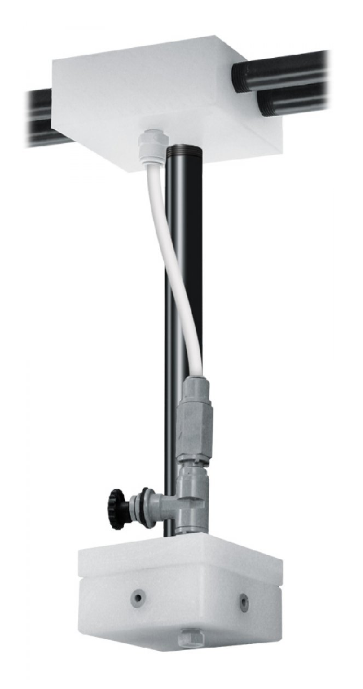
Our Pump Fed Fogger is a chemical atomizer receives ready-to-use chemical from a central
chemical feed system and uses compressed air to atomize the solution and project it as small to
medium size “damp” particles up to 15 feet in 4 directions. Fog (mist) fills the air and saturates exposed surfaces, including hard-to-reach areas. It is also available as a 2 or 8 way fogger.
Air and chemical solution flow can be activated manually or activated in multiple zones throughout your facility using PLC controllers. A needle valve can refine the particle size for your particular application and
manage chemical use and a check valve prevents excessive dripping after shutdown.
Includes
- Machined polypropylene ceiling manifold
- Machined polypropylene fogger body
- Chemical needle valve
- Chemical check valve